Søknadsfelt
Sprøytestøper er viktig prosessutstyr for produksjon av ulike industriprodukter. Med den raske utviklingen av plastindustrien og promotering og anvendelse av plastprodukter innen luftfart, romfart, elektronikk, maskineri, skipsbygging og bilindustri, blir kravene til støpeformer stadig viktigere. Jo høyere som kommer, de tradisjonelle formdesignmetodene kan ikke lenger oppfylle dagens krav. Sammenlignet med den tradisjonelle formdesignen, er datastøttet ingeniørteknologi (CAE) enten i form av å forbedre produktiviteten, sikre produktkvalitet eller redusere kostnader og redusere arbeidsintensiteten. I alle aspekter har de store fordeler.
Alle slagsCNC maskineringbrukes i bearbeiding av sprøyteformer. De mest brukte er CNC-frese- og maskineringssentre. CNC-trådskjæring og CNC EDM er også svært vanlig i CNC-bearbeiding av støpeformer. Trådskjæring brukes hovedsakelig i ulike typer rettveggsformbehandling, slik som konkave og konvekse støpeformer i stempling, innsatser og glidere i sprøytestøpeformer, elektroder for EDM, etc. For støpedeler med høy hardhet kan ikke bearbeidingsmetoder brukes, og de fleste av dem bruker EDM. I tillegg brukes EDM også til skarpe hjørner av formhulen, dype hulromsdeler og smale spor. CNC-dreiebenken brukes hovedsakelig til å behandle standarddeler av støpestenger, samt støpehulrom eller kjerner av roterende legemer, som sprøytestøper for flasker og bassenger, og smiingsformer for aksler og skivedeler. I formbehandling kan bruken av CNC-boremaskiner også spille en rolle i å forbedre prosesseringsnøyaktigheten og forkorte prosesseringssyklusen.
Former er mye brukt, og forming og bearbeiding av produktkomponenter i moderne produksjonsindustri krever nesten alle bruk av former. Derfor er formindustrien en viktig del av den nasjonale høyteknologiske industrien og en viktig og verdifull teknisk ressurs.Optimaliser den strukturelle utformingen av formsystemet og CAD/CAE/CAM til de støpte delene, og gjør dem intelligente, forbedre støpeprosessen og standardiseringsnivået for støpeformen, forbedre presisjonen og kvaliteten på formproduksjonen og redusere mengden sliping og poleringsoperasjoner på overflaten av de støpte delene og produksjonssyklusen; forskning og anvendelse av høyytelses, lettskjærende spesialmaterialer som brukes til ulike typer formdeler for å forbedre formytelsen; for å tilpasse seg markedsdiversifisering og produksjon av nye produkter, rask prototyping-teknologi og rask produksjon. Muggteknologi, som rask produksjon av formingsformer, plastinjeksjonsformer eller støpeformer, bør være utviklingstrenden for muggproduksjonsteknologi i neste 5-20 år.
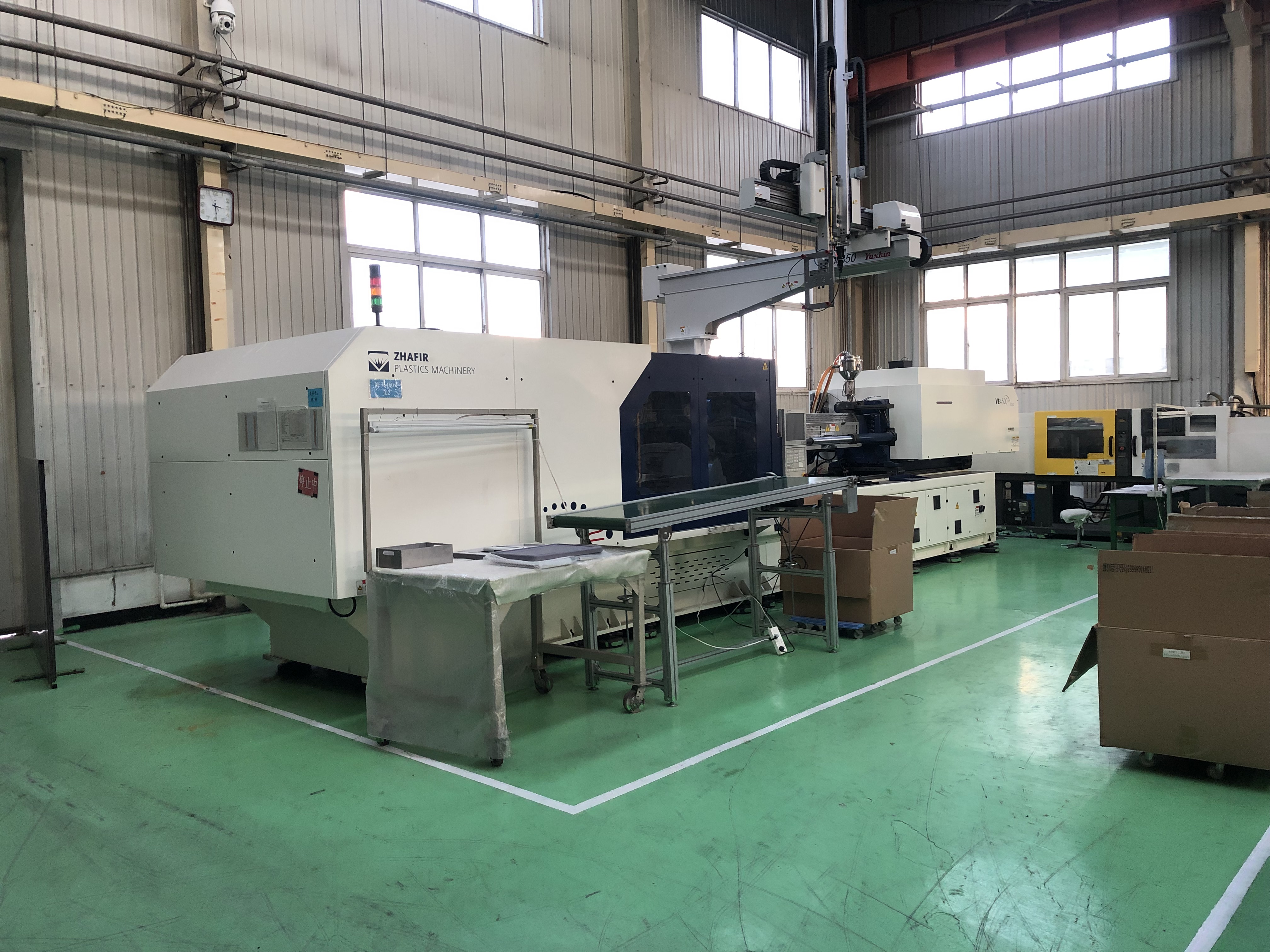
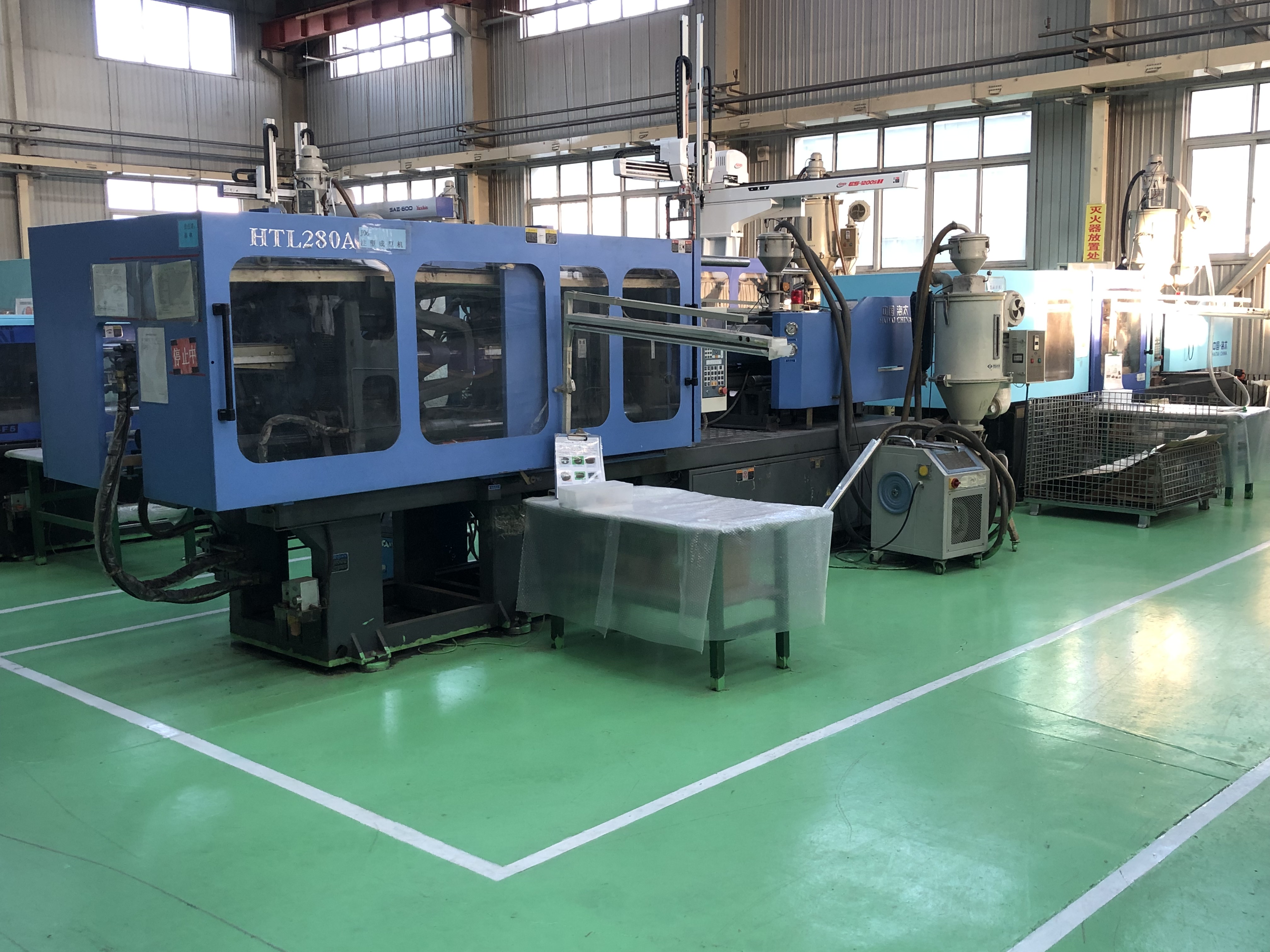
Platemetall er generelt definert som: metallplate er for metallplater (vanligvis under 6 mm) en omfattende kaldbehandlingsprosess, inkludert skjæring, stansing/skjæring/kompositt, bretting, sveising, nagling, skjøting, forming (som bilkarosseri). Dens bemerkelsesverdige funksjon er den samme tykkelsen på den samme delen.
For platebearbeiding er den enkle forklaringen at platebearbeiding er for platematerialer, for eksempel stålplater, galvaniserte plater og så videre for å bøye, skjære eller stemple dem til den angitte formen, for eksempel sirkulært tilbehør, buetilbehør og annen maskinvare , generelt brukt klippemaskin, bøyemaskin og stansemaskin.
Mekanisk bearbeiding er mer kompleks enn metallbearbeiding, hovedsakelig bearbeiding av deler, materialer er vanligvis blokker eller hele, men det er plater. Det er hovedsakelig å bruke profesjonelle prosesseringsmaskiner for skjærebehandling, som nå vanligvis brukes er dreiebenker, fresemaskiner, slipemaskiner, trådskjæring, CNC, gnistmaskin og annet prosessutstyr.
Platebearbeiding er enkel metallbearbeiding, for eksempel datamaskinkasse, distribusjonsboks, maskinverktøyet er vanligvis CNC-stans, laserskjæring, bøyemaskin, klippemaskin og så videre. Men maskinering er ikke det samme som bearbeiding av metallplater, det er ullembryomateriale som behandler deler, for eksempel maskinvaredeler av skafttypen.
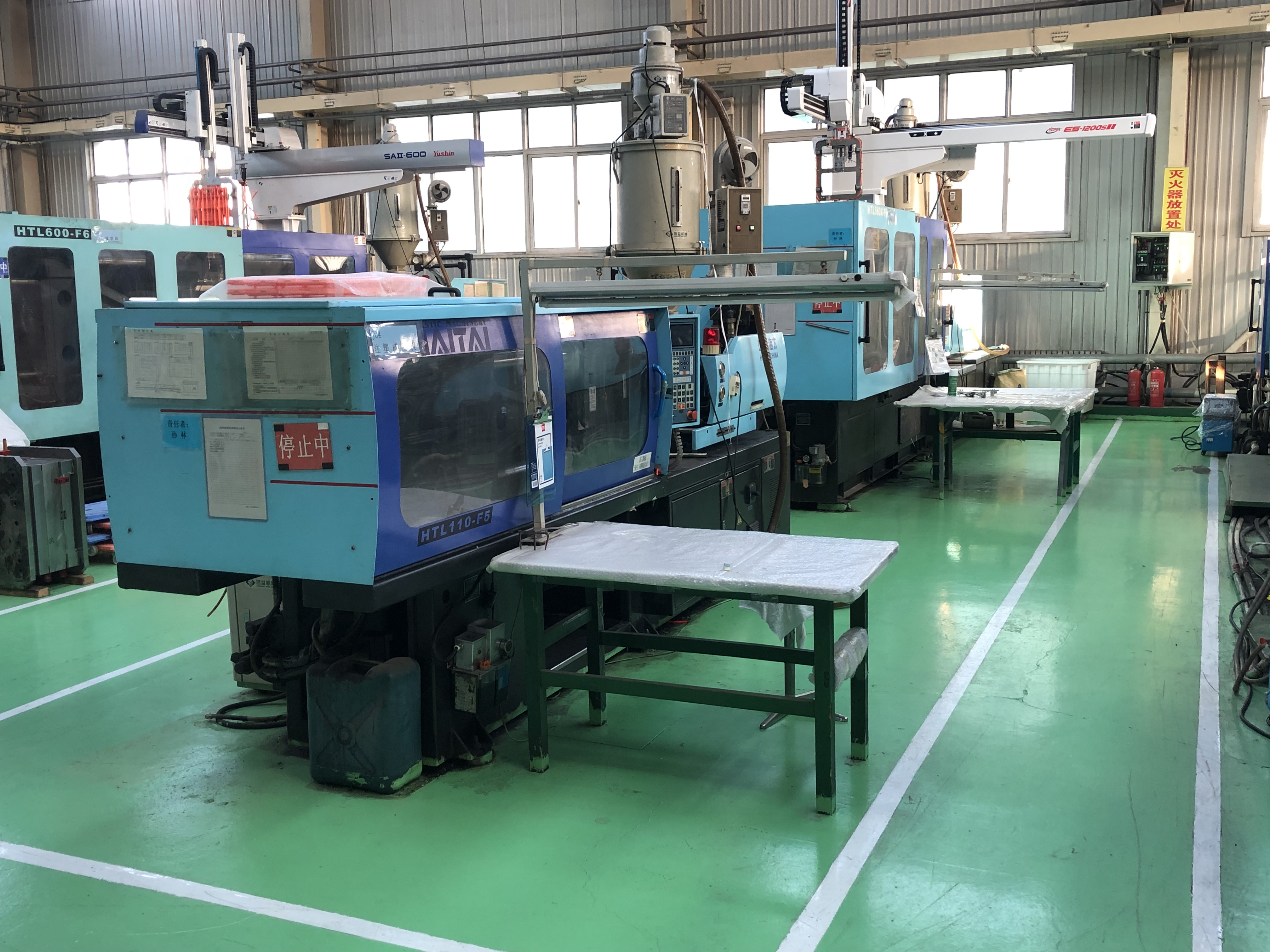
Innleggstid: 11. oktober 2021